Success stories
A few examples of parts that are difficult to produce
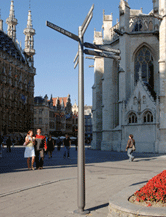
Project : Tourist direction indicator in AlSi12, length 1000 mm.
Series ~= 500 parts
Result : important flatness for machining the letters, which is a delicate operation with the part still being flexible when taken out of the mould. Particularly clean coarse surface skin despite the length of the imprint to be filled.
This enables direct electrostatic coating with powder paint without reworking the surface.
Projet : Suspension support for monorail in AS7G
Batch ~= 1000 parts
- Mould received from a dissatisfied customer (the parts break).
- Action: review of the design and casting system
Result
- Flawless part, which no longer breaks under a stress of 3000 daN.
- Before = melting of almost 3000 kg to make 1000 parts. After our design review = melting of 2024 kg.
- Gain ~= 1000 kg, approx . 30% energy saving (90 l. less heating oil).
- Markedly improved productivity.
Project : Casing for automated actuator, ~= 5 kg of AlSi9Cu3. Series ~= 1500 pts.
Very difficult part because of the thin wall (5mm) next to very thick walls (>40 mm). Substantial mechanical strength further to the substantial torque. Action: research effort and persuasion of the customer (Germany) to convince him to optimise the design of the part.
Result
- Quality obtained (sound and complete part).
- Gained the confidence of the customer who then entrusted the production of seven other parts to us.
Project : Flask for acoustic light (Schréder) in AS12 for metro station.
Batch ~= 1000 pairs
This was an urgent project. Little time for perfecting the design, no room for design errors, the part had to be waterproof. Optimisation of our design by numerical simulation of filling and solidification.
Project : "AGC" handle intended for the French Railways (SNCF), in AlSi12.
Series ~= 1000.
Result: Filling of a part whose thickness (2 mm) is at the limit of gravity casting, despite the complex shape of the part, with four stainless steel threaded overmoulded inserts.
Project : Railing base in AlSi7Mg
Result : We were able to form the particularly thin cover (2.5 mm), obtained with a fine casting skin. The strength of the base was verified and validated to meet the requirements of the standard.
Solution developed by ourselves to achieve the stipulated strength by avoiding the traditional expensive and energy-intensive solution of thermal treatment.